Research Projects
current and recent
Understanding the Corrosion of Heritage Iron
Preventing post excavation corrosion of archaeological iron is a challenge for heritage professionals worldwide. Apart from dry or deoxygenated storage, there is little evidence to show that other corrosion control methods are effective. Keeping objects dry is the easier and lower cost option, so the first question becomes: how dry do we need to get our storage and display environments? A second question asks: do factors such as chloride contamination mean that some objects need to be drier than others?
This AHRC funded project measured how fast Roman and Medieval iron artefacts corrode at humidities between 20-80% to gauge the level of risk to artefacts. This data was compared to the levels of chloride in the objects to assess the link between chloride and corrosion which revealed a complex and unpredictable relationship.
​
Thanks to this work, we now know that corrosion risk for iron is low below 30% relative humidity, increasing slowly up to 50% and very rapidly at higher humidities. This gives us a target for designing dry storage and determining whether objects can be displayed safely in museum environments.

Storage of Archaeological Metal Artefacts
When archaeological metals objects are excavated, they present an immediate problem. They may have been relatively stable in the soil but how can we stop them from corroding in the atmosphere? A parallel research project has show that drying the environment around metal artefacts is an effective way of preventing corrosion. What are the options for achieving this?
Millions of artefacts in museums and archaeological archives across the world are stored in plastic boxes with silica gel as a desiccant to dry the air inside. With endless options for choice of storage box and no evidence for how much silica gel to include, how can we set up the most effective and long-lasting microclimate? This project has investigated these factors to produce best-practice guidelines for the safe storage of metal small finds.
​
Whether your collection is large or small, the same principles apply and simple choices can dramatically affect the lifetimes of your artefacts. Access our detailed guidance on storage here.

Mary Rose Cannon Balls
Iron that has been excavated from marine archaeological sites is full of salts that drive its corrosion. For cast iron cannon balls, this can lead to spectacular break up. Although conservation treatments aim to remove the salts, how successful are they? How well do they prevent corrosion in the future when the objects are in storage or on display?
​
Henry VIII's ship, the Mary Rose, sank in the Solent in 1545. Excavation of artefacts began in 1979 with the hull of the ship finally being lifted in 1982. You can read more about the ship here. Among the excavated Tudor artefacts were more than 1000 cast iron cannon balls.
​
Treated in different ways by conservators over the years, this collection of cannon balls went on display in the new Mary Rose Museum in 2013. They were soon showing evidence of corrosion with some in danger of breaking up completely. Swift action removed the cannon balls from display to dry storage where they remain.
​
Our research, led by Jerrod Seifert, is establishing the safe display conditions for these cannon balls and examining whether the way they were treated in the past is influencing their stability today.
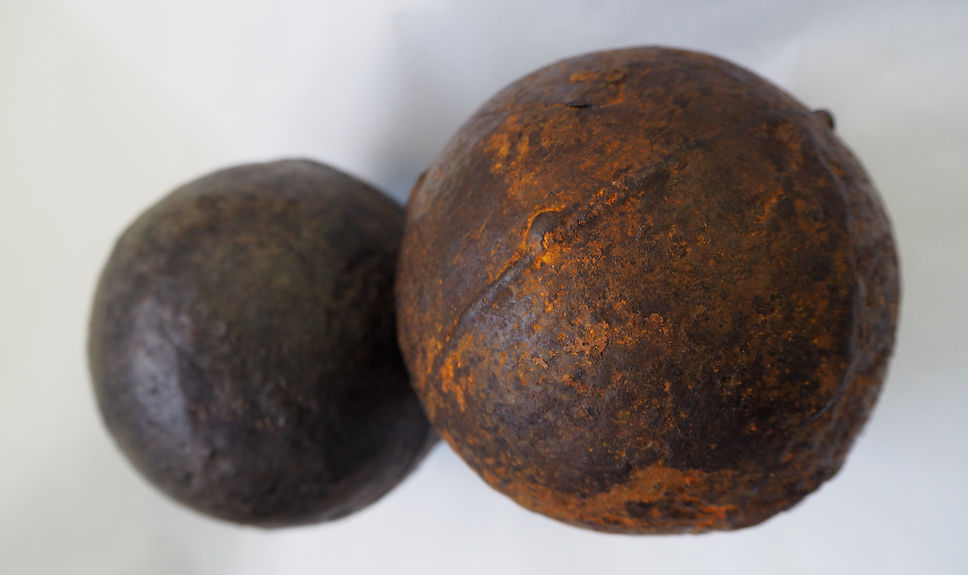
Identifying Instability in Copper Alloys
Chlorides from the burial environment can form cuprous chloride in archaeological copper alloy objects. After excavation, this compound reacts with humidity and oxygen in the environment forming voluminous corrosion products. These can break out of the smooth bronze patina as pustules and disruptive growths that disfigure the objects. Desiccated storage can prevent bronze disease from breaking out but identifying which artefacts are unstable due to cuprous chloride is complicated by similarities in appearance of several copper alloy corrosion products.
​
Johanna Thunberg’s research is addressing the difficulties that conservators and collections care professionals experience when establishing visually whether a copper alloy is suffering active corrosion or likely to. She is also examining the extent and rate of metallic copper lost to bronze disease and the efficiency of treatments which aim to reduce of prevent it.

Flame Cleaning of Historic Wrought Iron
Flame cleaning is a common treatment for heritage wrought iron. Applying a flame to surface of the ironwork combusts any existing coatings and spalls flakes of corrosion. Vigorous wire brushing removes any debris to produce a sound surface for recoating.
Although it is used often, almost nothing is known about how this treatment affects the iron and what that means for its long-term survival outdoors.
​
Working with blacksmiths and metalwork conservators, we are investigating how flame cleaning can be carried out without damaging the ironwork. Preliminary results can be found here.

Protective Coatings for Exterior Ironwork
Building on a previous project, PhD student Peter Meehan is carrying out real-time assessment of traditional and modern anti-corrosion coatings for historic wrought iron. He is using a range of techniques, including oxygen consumption corrosion rate determination, electrochemical impedance spectroscopy and spectrophotometry, to measure performance of the coatings on historic material in outdoor exposure. Ultimately, this will help in choosing coatings for structures such as historic gates, railings, bridges and other architectural elements.
​
Will Smith began an AHRC-funded project with English Heritage in January 2020. He is examining the influence of outdoor exposure environment on the corrosion and condition of modern artillery at exposed coastal sites around England. He will go on to investigate the performance of anti-corrosion coatings for the steels and other components of these artillery pieces to allow English Heritage to refine their treatment protocols.

Value and Risk in Running Historic Military Tanks
In collaboration with The Tank Museum, Bovington
Historic military tanks, dating from WWI to the recent past, form the basis of the collection at The Tank Museum, Bovington. The majority are on static display or in storage but a small number are maintained in working order and are run in hugely popular public displays.
Maintaining these running vehicles requires repair and replacement of original parts. Wear, tear and loss of historic materials must be accepted in the decision to display tanks in this way. How can we reconcile this with conservation ethics demanding that we preserve historic objects in perpetuity?
In her research, Luca Hoare is exploring the essence of historic tanks. What does it mean to experience a tank in motion with all of the associated sights, sounds and smells? Contemporary reports of tanks in military action lend weight to an argument that the essence of these vehicles is lost if the mechanisms of shock and awe, motion and sound, are lost to static display. Preserving the material then comes at the price of losing the essential properties of these dynamic objects.
​
